
The BMW Group heads the new circular economy project in the automotive industry: baptism Car2Carit focuses on materials such as aluminum, steel, glass, copper and plastic, and €6.4 million has been provided by the German Federal Ministry for Economic Affairs and Climate Action.
In this context, the German manufacturer joins forces with companies from the processing industry, raw materials processors and the scientific world to develop waysto improve the quality of secondary raw materials from disposal of used cars.
BMW: more recycled materials in cars
The BMW Group has set itself the goal of increasing share of recycled materials in cars of their brands to 50%compared to about 30% now.
To achieve this, BMW will rethink the way materials are recovered from end-of-life vehicles so they can be reused incircular economysubject to compliance with the quality standards of the group’s automaterials.
For the purposes of the Car2Car project, the BMW Group provides 500 vehicles failed, BMWs, Minis and other Rolls-Royces, be they thermal, hybrid or 100% electric. Project partners are exploring potential ways to improve sources of recycled transport materials.
BMW: artificial intelligence for the circular economy
The Car2Car Consortium works on quality, economic and environmental aspects of dismantling processes and post-shredding technologies to achieve an efficient circular economy. For this he calls on digital technologies etc’Artificial Intelligenceto automate and speed up the processing processes that were done manually until now.
The disassembly process, for example, can be partially automated through robotics and the integration of optical detection and sorting systems, as well as artificial intelligence. As such, the project is exploring ways to improve the quality and purity of recycled materials such as aluminum, steel, glass, copper and plastic.
So it allowsincrease the amount of secondary raw materials suitable for the production of new cars, while significantly reducing the processing work required to convert waste into raw materials for reuse, regardless of the materials used.
This project, led by the BMW Group, complements all the company’s initiatives processing of materials. The German group is the only car manufacturer that works independently processing center, since 1994 in Unterschleissheim near Munich. Processes up to 10,000 cars per year.
Source: Auto Plus
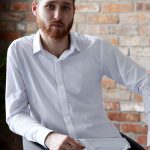
Robert is an experienced journalist who has been covering the automobile industry for over a decade. He has a deep understanding of the latest technologies and trends in the industry and is known for his thorough and in-depth reporting.