
One of the most polluting components of an electric vehicle is undoubtedly its traction battery. Indeed, it consists of many components that can pollute the environment if they are not recycled properly.
To help make the 100% electric vehicles in the Mercedes-EQ range more environmentally friendly, the German manufacturer will soon introduce battery processing plantwhich is currently under construction in Kuppenheim, Germany.
Mercedes processing plant: an innovative approach
It was during the ground-breaking ceremony that Mercedes provided more details about its state-of-the-art battery recycling plant, which aims to reduce the consumption of resources as well as creating a closed cycle of processing raw materials for batteries.
The first stage of factory production, as it is mechanical dismantling of batteries of electric vehicles should begin at the end of this year, 2023. In a few months, a pilot hydrometallurgical plant will be established to specify an innovative approach for integrated processing in one factory: the first in Europe.
Even if Mercedes does not specify the exact amount, several tens of millions of euros were invested in the construction of this plant, which is CO2 neutral. A project funded by the German Federal Ministry of Economics and Climate Protection as part of a research project. This investment marks an important step in Mercedes-Benz’s sustainability strategy, which is betting big on a 100% electric car.
Mercedes: produced more than 50,000 battery modules
Eventually, the Mercedes battery recycling plant in Kuppenheim will catch on all stages of the processing process from modular disassembly to grinding, drying and processing of battery materials.
Hydrometallurgical process, with a over 96% recovery rate, creates a true circular economy of battery materials. The entire battery recycling process is also taken into account within the framework of the comprehensive research project: from the development of logistics concepts, through the sustainable processing of valuable raw materials to the re-integration of secondary raw materials into the production of new batteries.
This pilot plant should have a annual capacity of 2,500 tons. Recovered materials will be reintroduced into the recycling cycle for production each year more than 50,000 battery modules for new Mercedes electric models. If the project is successful, production volumes can even be increased in the medium and long term.
Source: Auto Plus
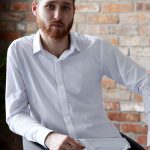
Robert is an experienced journalist who has been covering the automobile industry for over a decade. He has a deep understanding of the latest technologies and trends in the industry and is known for his thorough and in-depth reporting.