
The energy transition and electrification must also rhyme with the circular economy. And this last aspect necessarily includes reduce the use of raw materials and ensure efficient recycling of batteries. This is how Renault sees the future of electric mobility, and on paper the promises are obviously interesting.
Many manufacturers have adopted their own formula to achieve this goal, and Renault is undoubtedly one of the manufacturers most ahead of the curve. In fact, the brand intends to be the first European car manufacturer to start recycling batteries on an industrial scale.
Towards carbon neutrality from the beginning to the end of the chain
The developer’s idea can have many positive effects, and not only from an environmental point of view. The brand wishes to cooperate with various specialized companies extract and process lithium and other metals contained in electric vehicle batteriesthus creating a circular economy capable of generating billions of euros and reducing dependence on China and its raw materials.
According to Jean-Philippe Bauault, CEO of the TFIN project (for Future Neutral), “There is currently not a single person in Europe who can claim to recycle used batteries in a closed loop to extract nickel, cobalt and lithium for the production of new batteries”.
The use of recycled metals can also help lower the price of electric vehicles, given that the metals themselves make up 70% of the battery’s cost, and that these batteries make up 40% of the cost of an electric car.
And it is for this reason that Renault is betting heavily on its project, setting a target of 2.3 billion euros and an operating margin of more than 10% by the end of the decade.
Ampere, the new Renault laboratory
Batteries of the future will not only consist of recycled cells. Ampere, the brand’s electrification division, has announced the opening of a battery testing laboratory in Labre, a small town on the border of Luxembourg, Germany and Belgium. According to the press release, “The laboratory will play a strategic role in determining the best compromise between performance, cost, durability and safety of future batteries and anticipating technological advances in the field of cells”.
More than 120 devices for cell development and analysis will be installed on two levels in the 3000 m building2.
Several machines for the production of cell prototypes in a 600 m clean room2 it is planned to study the chemical composition of batteries and, thus, more accurately determine the duration and effect of frequent quick charges on batteries.
Source: Auto Plus
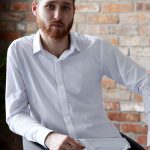
Robert is an experienced journalist who has been covering the automobile industry for over a decade. He has a deep understanding of the latest technologies and trends in the industry and is known for his thorough and in-depth reporting.