
We all know the destructive potential of electrical fires in any building. Not only are lives at risk, but property damage and downtime can be extremely costly.
Electrical fires cause 22% of workplace fires and are one of the leading causes of hospital fires (after food-related incidents). Electrical fires are often caused by faults in medium or low voltage wiring, switches or motors; insurance companies estimate that about 25% of all major electrical faults are due to loose or faulty electrical connections.
An unplanned production shutdown can result in a 5% to 20% loss in productivity. In terms of financial costs, research shows that 98% of organizations report that one hour of downtime can cost more than $100,000. Industrial manufacturers worldwide spend an estimated $50 billion annually on unplanned outages. They unexpectedly introduce additional maintenance, repair and replacement costs that can have a major impact on their business budget (source Henkel-Adhesives).
Fire prevention is the main reason many regulatory agencies require annual thermal surveys to reduce the risk of fire caused by faulty connections. Until recently, infrared (IR) thermography was used for these examinations. The method can be effective when applied according to regulatory documents, but requires inspections with a fairly low frequency.
Improper electrical connections are the main cause of failure in medium and low voltage installations. Improper torque, constant vibration, corrosion, excessive pressure or friction can damage cable connections, busbars and switches. Frequent temperature fluctuations and frequent starts/stops can further weaken the contacts.
The traditional approach to thermal inspections is to use infrared thermography, thermal cameras to inspect the highest risk areas of electrical equipment. This is usually done at regular intervals, such as every 12 months. Although the technology and process are effective when performed within these parameters, the method has several potential drawbacks.
Because inspections are only performed at certain intervals, personnel may not be alerted to the rapid deterioration of a particular connection point. Limited access to some electrical connections can lead to even greater risks that go unnoticed.
In contrast to thermographic surveys, continuous thermal monitoring is one of the most effective measures to prevent electrical fires, as it facilitates early detection of faulty connections, provides information on temperature alerts and reports for faster response.
Schneider Electric’s EcoStruxure continuous thermal monitoring solution includes self-powered wireless thermal sensors, the PowerLogic TH110 to help identify potential problems before they get out of control, the CL110 for temperature and humidity monitoring, and continuous thermal monitoring management software for all critical connections in the building such as cables and busbars. The software can be configured to send immediate alerts to the mobile devices of local operations and maintenance teams. The EcoStruxure platform also creates a preventive maintenance plan and thus reduces the potential risk of fire.
The CAPEX investment for a continuous thermal monitoring solution is typically less than 10% of the total cost of the electrical equipment.
Article based on Schneider Electric technology
Source: Hot News RO
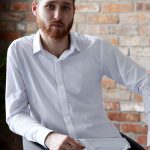
Robert is an experienced journalist who has been covering the automobile industry for over a decade. He has a deep understanding of the latest technologies and trends in the industry and is known for his thorough and in-depth reporting.